دانشنامه تخصصی فولاد و متالورژی : مرجعی کامل برای آموزش و آشنایی با فرآیندهای فولادسازی ، تجهیزات صنعتی ، استانداردها و نوآوری ها . اطلاعات بروز جامع درباره تولید و فرآوری فولاد در ایران و جهان
جستجو
پربحث ترين ها
-
دانلود کلید فولاد 2007
۹۴/۰۳/۲۳ -
تنها نرم افزار کلید فولاد اندروید
۹۴/۱۱/۰۳ -
-
آموزش نرم افزار کلید فولاد
۹۴/۰۳/۲۵ -
دیکشنری تصویری متالورژی
۹۴/۰۴/۰۷ -
-
الزامات آب و سوخت مجتمع فولاد
۹۵/۰۹/۲۳ -
-
-
ناحیه فولادسازی در شرکت فولاد مبارکه
مقالات فولادسازی مطالب علمی آشنایی با فولاد مبارکه معرفی کارنجات فولاد سازی
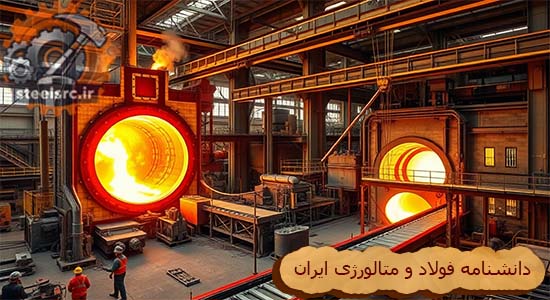
ناحیه فولادسازی یکی از 5 ناحیه تولیدی شرکت فولاد مبارکه است . وظیفه اصلی این ناحیه تولید شمش فولادی جهت تأمین ماده اولیه مورد نیاز ناحیه نورد گرم به مقدار و کیفیت
- فولادسازی مبارکه
توافق شده با آن ناحیه تولیدی می باشد .
ناحیه فولادسازی شامل واحدهای تولیدی بشرح ذیل می باشد :
- واحد حمل مواد Material handling
- واحد کوره های قوس الکتریکی Electric arc furnace
- واحد متالورژی ثانویه و آماده سازی پاتیل Ladle furnace treatment and Ladle Total service
- واحد ریخته گری مداوم تختال Continuous Casting of slab
- واحد آماده سازی شمش Slab cooling and conditioning
واحدحمل مواد :
اهم فعالیتهای قسمت :
- تحویل گیری و ذخیره سازی مواد
- بارگیری مواد در سیلوها جهت مصرف در کوره قوس
- انتقال و توزیع مواد جهت کوره های قوس ومتالورژی ثانویه
- بازیافت ضایعات فولادی و آماده سازی آهن قراضه
- کنترل قراردادهای خرید مواد مستقیم
الف) تحویل و توزیع مواد ورودی توسط نوار نقاله از ناحیه آهن سازی :
به منظور در دسترس بودن مواد و تضمین استمرار تولید آهن اسفنجی و افزودنی ها همانند آهک ، دولومیت و.... توسط نوار نقاله از ناحیه آهن سازی به ناحیه فولادسازی منتقل و در سیلوهای کوره قوس الکتریکی ذخیره می گردند ، که این واحد وظیفه کنترل و زمانبندی عملیات شارژ توسط نوار نقاله ها و انجام عملیات اضطراری تجهیزات مربوطه را بعهده دارد .
ب ) توزیع مواد افزودنی و مصرفی با سیستم های انبارداری :
دریافت ، انبارداری و توزیع حدود 24 نوع مواد در تناژها ، شکل و اندازه های مختلف در نقاط مختلف واحد تولید فولاد نیز توسط این واحد انجام گرفته وهمچنین در کنترل موجودی مواد مذکور همکاری لازم با قسمتهای مربوطه نماید .
ج ) آهن قراضه :
آهن قراضه آماده مصرف پس از تائید کنترل کیفی – ایمنی فنی از نظر مشخصات فنی توسط تأمین کنندگان با کمپرسی به محل حوضچه های ناحیه اعزام و جهت ذخیره سازی در 17 حوضچه مربوطه به ظرفیت تقریبی 45000 تن تخلیه می گردد . سپس باتوجه به دستورالعملهای مربوطه توسط جرثقیل در سبدهای مخصوص بارگیری و توسط ماشین حمل به داخل کارگاه جهت شارژ به کوره های قوس الکتریکی انتقال داده می شود .
د ) ضایعات :
با هدف مصرف مجدد ضایعات فولادی ، ضایعات تولید شده در ناحیه با مکانیزمهای پیش بینی شده به قسمت برش قراضه منتقل و پس از آماده سازی به حوضچه قراضه ها جهت مصرف ارسال می گردند .
واحد کوره های قوس الکتریک :
- دمش اکسیژن
- دمش گرافیت
- شارژ آهک و دولومیت جهت تولید سرباره پفکی
- نمونه گیری و اندازه گیری دما
مرحلة آخر در عملیات کوره های قوس عملیات تخلیه ( Tapping ) می باشد در این مرحله پاتیل خالی مذاب که دمای پیشگرم آن مطابق با دستورالعملهای تولیدی می باشد به زیر کوره هدایت شده و مقادیر مورد نیاز فروآلیاژ و مواد افزودنی مانند بوکسیت و آهک همزمان با تخلیه مذاب از کوره به داخل پاتیل بارگیری شده و ذوب تولیدی در پاتیل مذاب آماده تحویل به واحد بعدی میگردد. زمان کل ذوب از تخلیه ذوب قبلی تا تخلیه ذوب بعدی حدود 150 دقیقه به طول می انجامد و این عملیات بطور مداوم در این واحد در جریان می باشد .
واحد کوره های پاتیلی :
اهم فعالیتهایی که بر روی هر ذوب در LF صورت می گیرد به صورت زیر است :
- اکسیژن زدایی
- سرباره سازی
- تنظیم آنالیز شیمیائی
- تنظیم دما و زمان تحویل به واحد بعدی ( ریخته گری مداوم )
- تصفیه یا حذف آخالهای موجود در ذوب
اکسیژن زدایی :
سرباره سازی به اهداف زیر صورت میگیرد :
افزایش راندمان حرارتی قوس
- جذب آخالهای ذوب توسط سرباره
- سولفور زدایی بهتر
- کاهش خوردگی نسوز خط سرباره پاتیل
- جلوگیری از اکسیداسیون مجدد آلومینیم محلول در ذوب
- افزایش بازده و تنظیم راحتتر تنظیم آنالیز شیمیایی
- تمیز بودن پاتیل بعد از تخلیه ته پاتیل
- کاهش آلودگی صوتی
تنظیم آنالیز شیمیائی ذوب :
تنظیم دما و زمان تحویل به واحد ریخته گری مداوم :
تصفیه ذوب :
- ناخالصیهای اکسیدی (MgO , SiO2, Al2O3 و.... )
- ناخالصیهای کاربیدی ، نیتریدی ، سولفیدی
- ناخالصیهای فلزی و یا عنصر آلیاژی که بیش از میزان نیاز در ذوب موجود باشد .
- گوگرد و فسفر
- گاز مضر ( هیدروژن ، نیتروژن ، اکسیژن )
واحد ریخته گری :
عرض تختال تولیدی : از 650 میلیمتر تا حداکثر 1880 میلیمتر
طول تختال تولیدی : در دو نوع تختال بلند 10- 9/5 متر و تختال کوتاه 4/75 – 4/5 متر
ضخامت تختال تولیدی : 200 میلیمتر
پاتیل مذاب بعد از تنظیم دما و آنالیز شیمیائی در بخش متالورژی ثانویه توسط جرثقیلهای سقفی 300 تن به واحد ریخته گری منتقل می شوند که هر ذوب دارای یک شمارة 6 رقمی بوده که کلیه اطلاعات ذوب از جمله آنالیز شیمیایی ، دماها ، زمانها ، کیفیت و ... از طریق این شماره در سیستم MIS قابل ردیابی می باشد در واحد ریخته گری مداوم پاتیل مذاب ابتدا بر روی برج پاتیل گردان قرار می گیرد وپس از اتصال سیلندرهیدرولیکی به دریچه کشوئی پاتیل و تنظیم تاندیشکار روی خطوط ریخته گری جریان مذاب از پاتیل به تاندیش با بازکردن دریچه کشوئی شروع میگردد و سپس با بازکردن استوپر جریان مذاب به داخل قالب برقرار می گردد و با توقف چندین ثانیه ای ذوب در قالب جهت تشکیل پوسته منجمد شده اولیه ، استارت ریخته گری مداوم شروع می شود و با گذر شمش تشکیل یافته در قالب و در ادامه از مابین غلتکهای همراه با پاشش آب بر روی سطوح آنها جبهة انجماد در داخل شمش رشد نموده و در نهایت با رسیدن شمش به طول متالورژیکی ، بطور کامل در سطح مقطع تختال انجماد حاصل می شود و در ادامه با رسیدن
شمش به قسمت برش طول تختال و با در نظر گرفتن حداقل ضایعات در انتهای ریخته گری برش داده می شود و پس از خروج تختال از ماشین برش بوسیلة ماشین شماره زنی یک شماره 9 رقمی جهت شناسایی و قابل ردیابی بودن تختال بر روی آن حک می گردد .
با پایان ذوب اول ، ذوب دوم که بر روی بازوی دیگر برج پاتیل گردان قرار دارد گردانده شده و بر روی تاندیش قرار میگیرد و بلافاصله پاتیل باز می شود تا تداوم و پیوستگی ریخته گری حفظ شود . ذوبهای متوالی بطور متوسط حدود بیش از 5 ذوب در یک عملیات به شمش تختال تبدیل شده و تختالهای تولیدی جهت خنک سازی واصلاح به واحد بعدی تحویل داده می شوند .
واحد خنک سازی واصلاح شمش :
- خنک سازی با هوا
- خنک سازی با آب
تختال هایی که نیاز به خنک سازی آب دارند توسط میز غلطکی های موجود به دو تانک خنک سازی انتقال داده شده و توسط دو جرثقیل به صورت اتوماتیک به داخل تانک شارژ شده و تختال خنک شده (پس از حداقل20دقیقه ) از تانک خارج و به قسمت اصلاح تختال ارسال میگردد .
در قسمت اصلاح تختال ، تختالها توسط بازرسین کنترل کیفی بررسی و در صورت وجود عیوب سطحی آنها را مشخص می نمایند سپس اپراتورهای واحد اسکارف توسط مشعلهای دستی این عیوب را برطرف می نمایند و پس از تائید نهایی واحد کنترل کیفی تختالها به ناحیه نورد گرم انتقال داده می شوند ولی در صورت عدم تطابق با برنامه پذیرش ناحیه نورد گرم تختالها در انبار نگهداری و به تدریج به ناحیه نوردگرم فرستاده می شوند .
منبع : msc.ir
نظرات (۰)
هیچ نظری هنوز ثبت نشده است
پيشنهاد ويژه
طبقه بندی موضوعی
- معرفی کارنجات فولاد سازی (۲۲)
- مطالب علمی (۱۹)
- مقالات فولادسازی (۱۰)
- دانلود جزوه و پاورپوینت (۹)
- دانلود کتاب (۳۸)
- کتاب فارسی (۱۷)
- کتاب انگلیسی (۲۱)
- دانلود نرم افزار (۴)
- نرم افزار موبایل (۲)
- نرم افزار رایانه (۲)
- گالری (۱۲)
- دیگر موارد (۱۷)
- اخبار استخدامی (۱۰)
- معرفی کتاب (۳)
- عمومی (۴)
کلمات کلیدی
يادداشت سردبير
-
پیام به مخاطبین محترم
سه شنبه ۲۰ آذر ۱۴۰۳با سلام و احترام،
به اطلاع شما میرسانم که از این پس، فعالیتهای خود را در سایت جدید با عنوان ویکی فولاد به آدرس https://fooladwiki.blogfa.com ادامه میدهم.
از تمامی شما که در مدت فعالیت در سایت قبلی با من همراه بودید، سپاسگزارم و امیدوارم در وبسایت جدید نیز با مطالب و اطلاعات مفید، رضایت شما عزیزان را جلب نمایم.
شما میتوانید با مراجعه به سایت جدید، از مقالات و محتوای متنوع ما بهرهمند شوید. منتظر حضور گرمتان در ویکی فولاد هستم.
با آرزوی موفقیت و سلامتی....
آخرين مطالب
-
پیام به مخاطبین محترم
سه شنبه ۲۰ آذر ۱۴۰۳ -
آشنایی با اصول کار و ساختمان کورههای ذوب
شنبه ۲۸ بهمن ۱۳۹۶ -
فیلم معرفی شرکت فولاد خراسان
سه شنبه ۱۸ مهر ۱۳۹۶ -
مقاله کوره بلند
دوشنبه ۱۷ مهر ۱۳۹۶ -
کتابچه محصولات فولاد هرمزگان
يكشنبه ۱۶ مهر ۱۳۹۶ -
معرفی شرکت فولاد هرمزگان
شنبه ۱۵ مهر ۱۳۹۶ -
تصفیه پاتیل و گاززدایی تحت خلاء
چهارشنبه ۵ مهر ۱۳۹۶ -
استخدام شرکت صنایع فولاد کرمان (بردسیر)
چهارشنبه ۲۹ شهریور ۱۳۹۶ -
فیلم فولاد مبارکه - برنامه خسته نباشید
سه شنبه ۲۸ شهریور ۱۳۹۶ -
کلیپ معرفی شرکت فولاد کاوه جنوب کیش
چهارشنبه ۱ شهریور ۱۳۹۶
آخرين نظرات
پیوندهای روزانه
خبرنامه سایت
خلاصه آمار
چندرسانه ای
-
فیلم معرفی شرکت فولاد خراسان
سه شنبه ۱۸ مهر ۱۳۹۶ -
فیلم فولاد مبارکه - برنامه خسته نباشید
سه شنبه ۲۸ شهریور ۱۳۹۶ -
کلیپ معرفی شرکت فولاد کاوه جنوب کیش
چهارشنبه ۱ شهریور ۱۳۹۶ -
گالری عکس کارخانه فولادسازی_فولاد آلیاژی ایران
جمعه ۵ تیر ۱۳۹۴ -
فیلم معرفی شرکت فولاد آلیاژی ایران
پنجشنبه ۴ تیر ۱۳۹۴ -
معرفی فیلم مجتمع فولاد اسفراین
پنجشنبه ۲۸ خرداد ۱۳۹۴ -
دانلود انیمیشن خط تولید شرکت فولاد مبارکه اصفهان
پنجشنبه ۲۱ خرداد ۱۳۹۴